Zero carbon, zero waste
How can a sustainable manufacturing process support circularity in the flooring industry? Find out how Forbo Flooring reduces carbon emissions and waste during the production and distribution process.
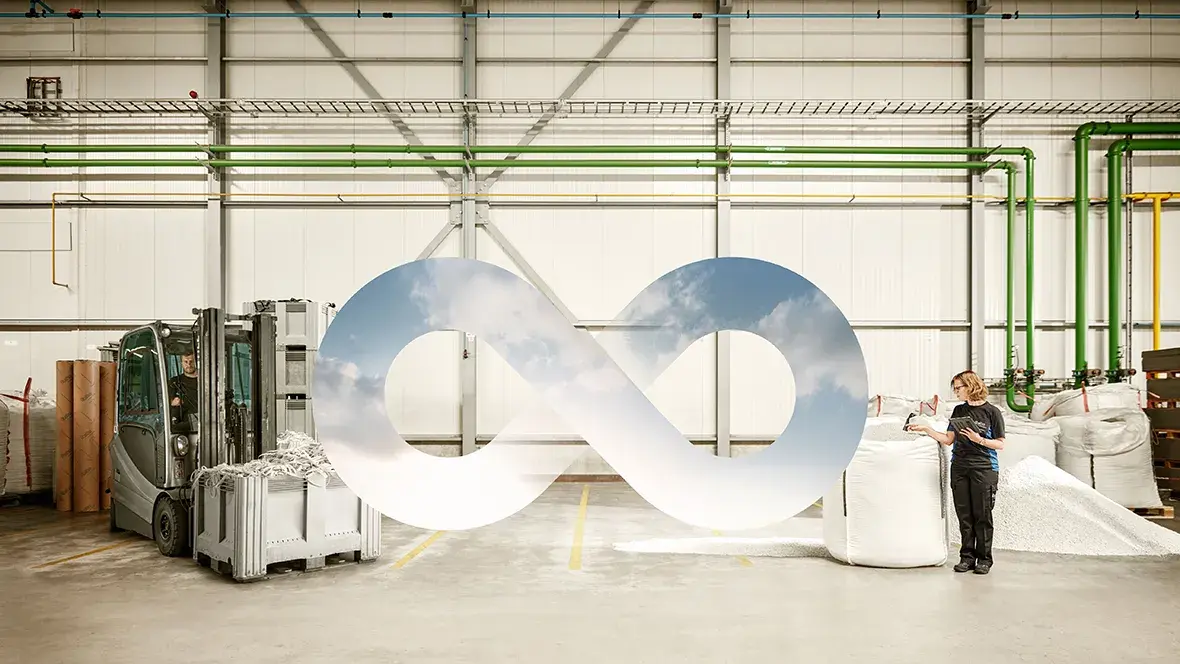
Design for reuse: that is our mission here at Forbo Flooring. With the planet’s resources vanishing quickly, it is of ever-growing importance to ensure a circular economy, where products are developed and manufactured to be recycled and reused for a new lease of life.
There are five main aspects to be considered when designing circular flooring. So far in this series, we have looked at the role of design and sourcing when it comes to circularity. But when we think about a sustainable future, the cycle doesn’t stop here. In this post, we take a look at the role the production and distribution process has in circular flooring.
CO2 emissions, electricity usage, waste production: these are just a few aspects of manufacturing which have a huge impact on our planet. According to a report by the Climate Change Committee (CCC) from 2020, manufacturing itself represents 90% of the manufacturing and construction sector’s emissions.
This shows that simply choosing sustainably sourced building materials is not enough. A sustainable supply chain cannot work without sustainable manufacturing. The carbon footprint of production needs to be taken into consideration as well. On top of that, energy usage and waste production are two big factors, amongst others, which contribute to the deterioration of the planet.
Forbo Flooring has 11 manufacturing sites in seven countries. All of them are ISO certified and follow our sustainability program for a carbon neutral and zero-waste production. As part of this strategy, we follow the 5Rs: redesign, reduce, reuse, recycle and renew.
Take our linoleum factories, for example: The vast majority of linoleum waste, such as installation residues, is reused in Marmoleum flooring products. The focus for our vinyl floor coverings lies on improving recycled or reused content as well as using advanced waterborne lacquers and dyes without any harmful substances.
And whilst our Tessera tiles are made from 60% to 75% recycled content by weight, our Ripley factory boasts a one-of-a-kind, on-site recycling plant. Around 86% of the factory’s own waste is processed, recycled, and reused each week, amounting to almost 50 tonnes of waste per week – or 2,600 tonnes per year. Any cutting waste material, leftover tiles, planks, and vinyl are collected and recycled in the factory itself, and then reused as a sublayer in new Flotex products.
In 2023, 78% of our production waste was reused or recycled. In 2023, the weighted average amount of recycled and reused content in our flooring products was 37%. If we can’t recycle it within Forbo Flooring, we pass it on to external recycling sites who can give the waste a new lease of life, for example in the form of traffic cones.
Additionally, we use 100% renewable energy sources whenever possible. Even though we’ve seen a shift towards heavier commercial products – whose production requires more energy – we have seen an almost equal level of energy consumption between 2017 and 2024. This is due to our implementation of a better monitoring system and energy saving programs.
Of course, a crucial point is CO2 emissions. Between 2004 and 2023, the average CO2 emission per square metre of product dropped by a whopping 77%. At our manufacturing sites, the emissions are 1:1 in relation to the energy used. But to reach our goals, we need zero carbon credits – and we won’t stop until we get there.
Our aim is clear: we want to further reduce on-site CO2 emissions, achieve total renewable electricity usage, become a zero-waste company, and ensure that all products contain recycled content, preferably post-consumer. We are actively contributing to this by starting pilot projects in which we recycle post-consumer floor coverings as well as loose-lay floor covering products.
In 2019, we initiated a three-year rolling programme to replace the three afterburners at our Coevorden facility, which made up the largest proportion of natural gas dependency at the plant. We have since then replaced two afterburners with static filters and gas-fired thermal oil heaters, cutting the CO2 emissions for fume eradication by 25%. The third afterburner is replaced in 2023.
Furthermore, we are looking into improving our transportation systems, from and between plants all the way to the end-consumer. We combine different products in one truck, which decreases the number of vehicles needed, improves lead times and reliability, and makes planning a lot easier. We also aim to ship containers and products by barge and rail, where possible, to optimise CO2 emissions.
Forbo products aim to be as green as possible – from design to end of life. Find out in the next part of this series how Forbo ensures a long life-span and easy maintenance for each and every product.