Linoleum Forbo: buono per natura.
Se prodotto nel modo giusto come fa la Forbo, il linoleum cattura una quantità maggiore di CO2 di quante siano le emissioni.
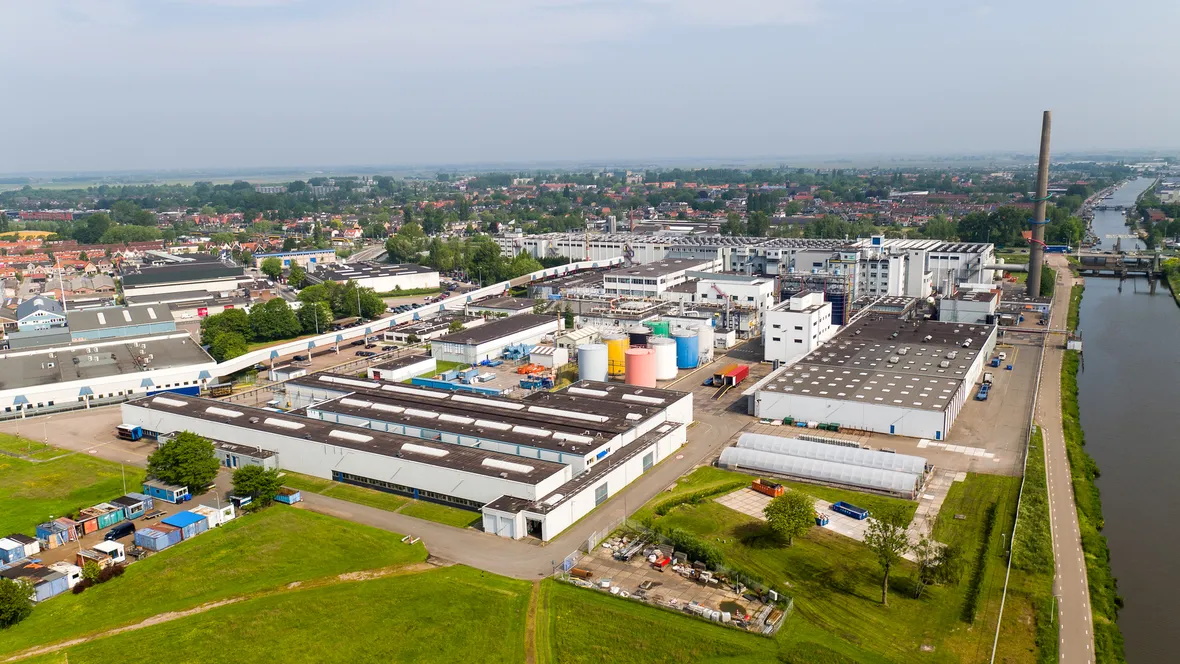
Chiunque percorra la strada tra Amsterdam e Alkmaar, è circondato da distese di campi e canali che rendono ancora più suggestiva la ciminiera in disuso presso l’uscita dell’autostrada di Assendelft. «È veramente una pietra miliare», dice Bregje Smulders. «Anche se in effetti non è mai stata usata». La fabbrica di linoleum più grande e più moderna al mondo, a poco meno di mezz'ora a nord-ovest di Amsterdam, è dove la Forbo, leader mondiale di settore, produce centinaia di migliaia di classici pavimenti in linoleum ogni anno, con il marchio Marmoleum. Bregje Smulders, Product Manager del reparto linoleum, è anche responsabile della sostenibilità ambientale del prodotto e spiega come l’impianto abbia introdotto importanti innovazioni nella produzione affinché Marmoleum abbia un impatto CO2 neutro sull’ambiente (dalla raccolta delle materie prime ai cancelli della fabbrica).
OGNI METRO QUADRATO DI PAVIMENTO MIGLIORA L’AMBIENTE
Le fabbriche di tutto il mondo rilasciano nell'aria tonnellate di biossido di carbonio (CO2), che è nocivo per l’andamento del clima. Dal 2018, la produzione di pavimenti Marmoleum nella fabbrica di Assendelft ha un impatto neutro di CO2. “Secondo i calcoli, facciamo addirittura di meglio: ogni metro quadrato di Marmoleum sottrae 40 grammi di biossido di carbonio dall’ambiente”, dice Markus Baum, Technical Product Manager della Forbo.
“Da allora, alcuni dei nostri prodotti sono persino migliorati”, aggiunge Smulders. Questo grazie alla filosofia aziendale e al linoleum stesso. Tutto nasce dal fatto che il 97% di Marmoleum è fatto di materie prime naturali, delle quali il 62% sono rinnovabili in tempi brevi, anche con raccolto annuale. Un pavimento resistente e duraturo che è ecologico e sostenibile per l’ambiente. “Se il linoleum fosse inventato oggi, sarebbe probabilmente l’invenzione del secolo”, dice Bregje Smulders.
Il 97% del linoleum è fatto di materie prime naturali. L’elemento principale è l’olio di semi di lino che, mescolato con la resina di pino e riscaldato, produce il cosiddetto cemento di linoleum. Dopo aver aggiunto farina di legno e pietra calcarea finemente macinata, il cemento di linoleum è calandrato su una tela di iuta larga 2 metri, che serve come strato di supporto (ancora una volta) naturale per il Marmoleum. Un grande assortimento di pigmenti colorati garantisce infine una varietà di splendide visuali.
L’impianto Forbo di Assendelft, a nord-ovest di Amsterdam, in Olanda, è la fabbrica più moderna e sostenibile di linoleum al mondo: il processo di produzione usa il 100% di energia verde, proveniente da fonti rinnovabili, come energia solare ed eolica.
Oggi, gran parte delle fasi di produzioni è automatizzata e solo le grandi fotografie in bianco e nero appese alle pareti della fabbrica testimoniano del lavoro manuale del passato ad Assendelft. Le materie prime di Marmoleum, invece, non sono cambiate molto. Il linoleum contiene il 19% di olio di semi di lino, una pianta che si rinnova rapidamente. Il suo raccolto assorbe 1,6 kg. di gas serra per ogni metro quadrato di linoleum. Altri ingredienti sono la iuta, la resina di pino e la pietra calcarea finemente macinata: tutti ingredienti che si trovano in natura. A questi ingredienti si aggiungono farina di legno e tallolio, scarti riciclati dall’industria del legno e della carta. Circa il 44% degli ingredienti usati per produrre Marmoleum proviene da procedimenti di riciclo.
Tutto può essere sostenibile, basta volerlo
Appena all’interno dei cancelli della fabbrica, sono situati i silos dove viene stoccata la farina di legno proveniente dalla Germania del nord. L’olio di semi di lino arriva navigando lungo gli ampi canali che, da Amsterdam ad Alkmaar, attraversano le distese di campi olandesi. Dal 2013, la Forbo ha ridotto del 31,5% le emissioni di CO2 imputabili alla logistica, senza modificare gli itinerari. Abbiamo acquistato furgoni ecologici e tutti i trasporti interni alla fabbrica sono su veicoli elettrici. Il trasporto dei rotoli di linoleum dalla fabbrica al magazzino è senza emissioni, grazie al nastro trasportatore sospeso lungo 750 metri. Anche i nostri fornitori usano metodi sostenibili. Un tempo, per ottenere la farina di legno, si usavano fonti energetiche tradizionali, mentre oggi si usa energia eolica o solare. La Forbo stessa ha installato pannelli solari nei tre nuovi magazzini, che hanno ottenuto il Certificato Gold della LEED. Da dieci anni, la produzione utilizza al 100% energia verde. “Abbiamo fatto grandi miglioramenti qui” dice Smulders mentre saliamo la scala metallica che porta all’edificio dove l’olio di semi di lino e la resina sono lavorati per ottenere il cemento di linoleum. ‘Si tratta soltanto di prendere la decisione giusta”. Il cemento di linoleum sta bollendo nelle gigantesche caldaie, insieme alla pietra calcarea, un procedimento che, naturalmente, utilizza anche qui energia verde. Si forma il cemento di linoleum, che ha la consistenza della gomma da masticare, di colore brunastro o color ambra. Il cemento di linoleum costituisce il 30% del prodotto successivo.
Ossidazione a calandratura
Utilizzando energia verde, l’olio di semi di lino e la resina di pino sono messi a bollire in grosse caldaie. L’ossidazione della resina e dell’olio di semi di lino produce il cemento di linoleum, una massa calda e gommosa. Affinché questa massa non sia eccessivamente appiccicosa, si aggiunge la polvere di pietra calcarea in uno strato sottile.
Pietra calcarea e farina di legno sono usati come filler; la iuta fornisce il supporto del linoleum e i pigmenti sono aggiunti per dare la colorazione. Infine, il linoleum è calandrato al supporto, lasciato nelle camere di essiccazione per due settimane e rifinito con il finish protettivo a raggi UV.
ALTRI MIGLIORAMENTI
I teli, lunghi un chilometro, sono trasportati nelle camere di essiccazione e gli esperti stabiliscono quando saranno pronti per la spedizione. Si tratta di una scienza esatta ed è la fase a maggior consumo energetico, con la necessità di temperature altissime per scaldare stanze di 20 metri di altezza. L’energia solare non è sufficiente: “Usiamo anche gas naturale”, spiega Baum. Qui si può migliorare, per diventare ancora più ecologici. Sono state installate apparecchiature che misurano il consumo energetico in alcune delle 56 camere di essiccazione.
Il cemento di linoleum è fatto maturare, un procedimento che rilascia una grande quantità di calore, con temperature che, nonostante questi locali siano senza riscaldamento, superano i 30ºC, abbastanza per scaldare altre zone della fabbrica. Il prodotto ha ora un colore brunastro, a volte chiaro come il caramello, a volte scuro come il cioccolato. Il colore definitivo del linoleum si otterrà solo più tardi, con l’aggiunta dei pigmenti.
I teli finiti di Marmoleum sono appesi ad asciugare e qui il calore necessario è ottenuto con impianto a gas. Gli specialisti, con grande abilità e sensibilità, devono stabilire quando i teli di Marmoleum sono pronti.
Per garantire una perfetta aderenza tra lo strato di linoleum e il supporto di iuta, aggiungiamo uno strato granulare composto in maggior parte da materiale riciclato pressato tra i due componenti principali. Un carrello elevatore trasporta il materiale alla calandra.
Tutti i veicoli della fabbrica sono azionati elettricamente. I rotoli di linoleum sono convogliati al magazzino, a 750 metri di distanza, anch’esso azionato con energia elettrica rinnovabile. per mezzo di un sistema sospeso su rotaia. Il prodotto finito è traportato in alto, sopra le teste dei dipendenti, completamente ecologico.
“L’intero procedimento sarà ulteriormente migliorato” dice Smulders “In futuro, potremo dimezzare il consumo energetico”. Quando è finalmente pronto, il linoleum è rifilato, tagliato a misura e imballato, per poi essere inviato al magazzino totalmente automatizzato. Il magazzino ospita un totale di 110.00 rotoli di 60 m² circa ciascuno. Alcuni rotoli provengono dall’impianto di Kirkcaldy, in Scozia, la seconda (e originaria) fabbrica di Linoleum della Forbo.
In Scozia, i rotoli di linoleum sono stoccati nel più moderno dei tre magazzini, dotato di pannelli solari. Questo sito ha conseguito il Certificato “Gold” della LEED (Leadership in Energy and Environmental Design) come edificio particolarmente ecologico. “Vogliamo essere d’esempio ovunque”, dice Bregje Smulders. Dalla hall, che ha l’aspetto di un grosso cubo verde, si può vedere la vecchia ciminiera all’estremità dell’enorme area della fabbrica.
Oltre che per realizzare pavimenti di qualità, il linoleum è usato come superficie per arredi, porte, pareti e per realizzare i pannelli per bacheca della collezione Bulletin Board.
Texsti Robert Otto-Moog / Fotografia di: Matthias Groppe, Paderborn