Process
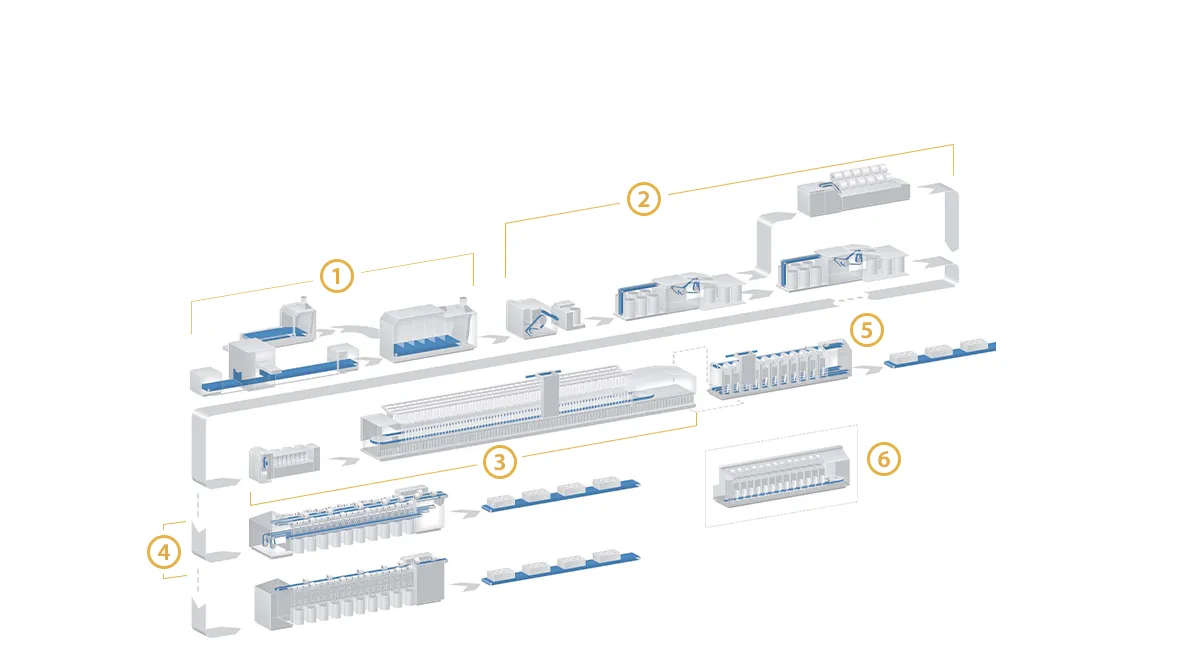
In the spinning mill, yarn manufacturing starts when the raw fibers (cotton, wool or synthetic fibers) are delivered in bales. First of all, a bale opener loosens tufts from the raw bales. Bale opening can be manual and automatic. When bales are opened automatically, a bale cutter removes the tufts from the raw bales, which are stacked next to one another. A vacuum and the downstream pipes convey the tufts to the next step in the process. In automatic bale openers, the purpose of the conveyor belts is to cover and therefore seal the suction channel. When bales are opened by more compact hopper feeders manually, the raw bales are loosened mechanically and their blend is already very precise.
Once the tufts have been cleaned and foreign bodies removed mechanically, the tufts are combined and mixed in the blender. Blending the tufts homogenizes the subsequent yarn quality.
Technical requirements for the belts
Automatic bale openers require belts that are exceptionally laterally stiff, but longitudinally flexible so that the vacuum channel is sealed reliably. In more compact hopper feeder bale openers, fibers must be fed reliably to the opener rollers/belts without fiber accumulating. Conveying synthetic fibers that differ in terms of moisture and where yarn lubricant has been applied in hopper feeder bale openers and blenders, requires the conveyor belt coating to have a dirt-repellent surface and chemical resistance.
Our solution
Certain Siegling Transilon conveyor belts offer the ideal solutions for this process. Due to its surface quality and lateral stiffness, a polyamide belt is predestined to cover the suction channel during automatic bale opening. Depending on the belt design and coating chosen, Siegling Transilon conveyor and processing belts are antistatic, resistant to oil and grease and their surface quality is so high that the material is conveyed reliably and gently. Siegling Transilon belts stand out for reliable belt tracking, durability and the ease with which they are fitted.
Once the fibers have been cleaned and blended, they are carded. Carding involves separating out the tufts down to individual fibers and aligning them so that they are parallel between a drum and revolving needles. This produces a wide, fine web which is joined together at the card take-off to form what’s called the sliver and deposited in drums for in-plant transport. To ensure the blends are as similar as possible, the can s are then intermixed and the slivers that have been removed are doubled. This takes place before the sliver is treated. The slivers are stretched on breaker and autoleveler draw frames and placed in a drum again. The result is even greater fiber parallelism, uniformity and tensile strength of the sliver, which is now thinner as a result of the drawing process and is generally referred to as draw frame sliver or roving.
A further improvement in yarn quality can be achieved by optionally adding a combing process downstream when processing wool (worsted yarn) or long-staple cotton fibers.
Technical requirements for the belts
When used for drives, reliable transmission of sometimes significant circumferential forces with different damping properties is required. At the same time, the power transmission belts must operate as quietly as possible and be durable. In the case of the cross-take-off belt in the card, the belt surface must be able to remove web continually and gently. No fibers may be allowed to build up on the belt surfaces at any time.
The power transmission belts in draw frames must be suitable for cross- and angle-drives and ensure uniform and vibration-free power transmission to the draw frames.
Our solution
Siegling Extremultus power transmission belts guarantee the transmission of high circumferential forces, e.g. for cylinder drives in cards. Elastic machine tapes convey the web gently to the drum.
In order to be wound non-destructively onto the ring frames’ roving bobbins, the rovings must not rotate too much on the flyer. During ring spinning, this roving, which is still capable of warping, is then stretched more finely and immediately afterwards spun evenly at a high twist into a tearproof yarn. A small metal bracket, the ring traveller , rotates on a circular guide, the spinning ring, around a spindle, winds the yarn onto a tube and forms the cop. The required ring yarn characteristics, such as yarn count and twist, for natural and man-made fibers can be set by varying the degree to which the roving is drawn, the rotational speed of the spindles and the diameter of the ring traveller.
Technical requirements for the belts
Fast spindle speeds mean the belt surface has to provide consistently good grip for the sometimes low arcs of contact and tangential drive types. At the same time, the spindle drive belts’ tension must remain stable and they need to be durable despite a lot of bending cycles.
Our solution
The highly abrasion-resistant Siegling Extremultus tangential belts’ elastomer coatings don’t become tough (the surfaces don’t vitrify/harden) and they maintain a constant friction coefficient after the running-in phase. As a result, belt velocities of up to 38 m/s can produce consistent spindle speeds. Thanks to the exceptional customized belt characteristics, the yarn quality remains the same throughout the belt’s service life.
Special conveyor belts and machine tapes with different characteristics, i.e. troughing capability or good grip, ensure that material flow is reliable and guarantees productivity when empty reels or cross-wound bobbins are conveyed.
The GG 20E-20 tangential belt and UT 8E spindle tape with a polyester tension member can be made endless with a Z-splice quickly and easily. Adhesives are not required. Siegling Extremultus tangential belts and spindle tapes for ring frames both remain antistatic. The spindle tapes for 2- and 4-spindle drives have abrasion-resistant polyurethane coating on the side facing the drum and an impregnated, wear-resistant version on the whorl side.
Efficient and automation-friendly OE (open end) rotor spinning is primarily used for short to medium staple cotton and various man-made fibers such as viscose, polyester and polyamide fibers. The most well-known types of yarn are terry cloth and denim for jeans.
The OE spinning process combines spinning and winding and, in contrast to ring spinning, does not require roving. During OE spinning, the draw frame sliver in cans is broken down to individual fibers by an opening roller and then formed into an accumulation of fibers by centrifugal forces in the groove of a high-speed rotor at the open fiber end. When drawn off via a stationary draw-off nozzle, the end of the yarn rotates around its axis and continuously turns (spins) the open fiber ends that have accumulated in the rotor groove. The resulting rotor yarn is continuously drawn off through the draw-off nozzle, treated with paraffin if necessary and finally wound up into a cross-wound package and conveyed off.
Technical requirements for the belts
Uniform rotational speeds and short start-up times are required for the very high rotor speeds. The tangential rotor drive via delicate twin-disc bearings requires the belt to operate without any vibrations and the belt coatings to have a friction coefficient that is as consistent as possible throughout the belt’s service life. Furthermore, in order to ensure superior durability, rotor-driven belts must have stable tension, be equally thick and exceptionally resistant to abrasion. Depending on the type of conveying required, different belt properties are required to take dirt and cross-wound packages away.
Our solution
The highly abrasion-resistant elastomer coating on Siegling Extremultus rotor and opening roller belts does not vitrify/harden and maintains a constant fiction coefficient after the running-in phase. As a result, belt speeds of up to 70 m/s and short start-up times, as well as consistent rotor speeds, are possible. Better yarn quality is achieved over the whole of the belt’s service life. A variety of specialized conveyor belts with different characteristics ensure reliable and productivity-enhancing material flow (to convey dirt and cross-wound bobbins away).
In the spinning mill, several cops are wound onto a slightly tapered tube on winders called coners. The resulting cross-wound package can then be used as master package for twisting machines, looms or knitt ing machines. In order to increase the level of automation in this process, the coners are often linked directly to the ring frame. After doffing, the cops are positioned on trays on the ring frame. These trays are transported to the winding stations via several conveyor belt lines with switching systems. A cross belt then feeds each of the cops to the next empty rewinding station. Automatic splicers (yarn joining devices) boost the fiber coners’ exceptional level of automation. After changing cops or if yarn breaks, these devices automatically join the open yarn ends. Finished cross-wound packages are expelled by a mechanical ejection system and onto a slightly troughed conveyor belt. This cross-wound bobbin discharge conveyor finally transports the bobbins to the palletizing and packaging station.
Technical requirements for the belts
Due to the switching systems along the conveyor belt sections, conveyor belts with constant good grip and accumulation capacity are required. Short tensioning stations require greater and more uniform tension and elongation in the conveyor belts used in order to guarantee non-slip grip and therefore exact positioning of the trays.
Our solution
Conveyor belts with characteristics specific to the application, such as stable tension, very good tracking and surface properties, ensure reliable and productivity-boosting conveying of the trays and gentle removal of the cross-wound packages.
Twisting is a yarn finishing process in which two or more spun yarns or several twisted yarns are usually twisted together in opposite directions (S and Z twists). Both natural fiber yarns and man-made fiber filaments are twisted to achieve greater tensile strength, e.g. for tire cord fabrics, or to achieve attractive fashionable effects (novelty yarns).
Double twisting is the twisting process most frequently used. On the two-for-one twisters, two roving bobbins on top of one another in a stationary spindle pot are slotted onto a hollow spindle. The yarn wound on the roving bobbins runs from the top through the spindle to the bottom. From there it runs along the outer wall of the spindle pot to a thread guide and finally to the take-up device at the head of the machine. Each time the spindle rotates, the yarn twists once between the roving bobbin and the tip of the hollow spindle and a second time between the bottom of the lower spindle and the thread guide.
Spindle speeds of up to 15,000 rpm can be achieved on very efficient two-for-one twisters for staple fiber yarns.
Technical requirements for the belts
In order to achieve uniform spindle speeds, the tangential belts must have consistently high grip and good resistance to the yarn lubricants used in the twisting process. The high level of power transmission needed requires belt tension to be exceptionally stable and the coatings to be very abrasion resistant.
Our solution
Siegling Extremultus GG 30E-30 or GG 30P-32 as power transmission and tangential belts.