100 Years
1919 - 2019 | Constantly innovative
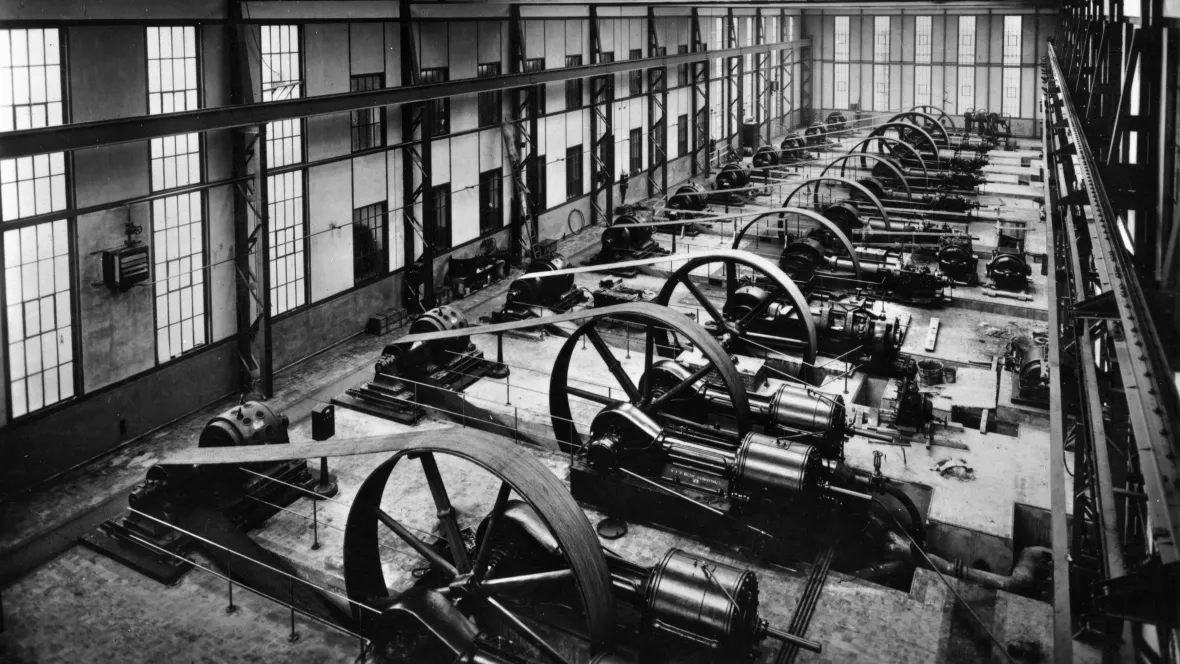
Ernst Siegling founds the company in Hanover, Germany. Chrome leather upright belts and other
innovative power transmission products go into production.
Successful launch of the first flat belts with adhesive coatings and the first electrically conductive belts for spaces with an explosive risk.
Invention of the first multilayer flat belt made of nylon and chrome leather, patented under the Extremultus brand name.
Hellmut Siegling (1922 – 2006), son of the company’s founder, takes over as the company’s CEO.
Construction of a new plant and start of production in Hannover-Vahrenheide.
Foundation of EXTREMULTUS, Inc. with sales and fabrication facilities on Long Island, N.Y. (USA). Relocation to Englewood, N.J. in 1960.
An idea is born regarding a conveyor belt for light materials handling: a new product line is developed bearing the Transilon brand name.
A second plant is constructed in Garbsen as a fabrication facility.
Transilon conveyor and processing belts go into production at the plant in Fukuroi, Japan. (The production facility is extended in 1982).
Launch of the new Siegling logo.
Production is started at the Carolina Manufacturing Center (CMC) in Huntersville, N.C. (USA).
Swiss corporation Forbo International SA take over shareholder interest.
The plastic modular belts go into production under the Prolink brand name.
The Forbo Siegling (Shenyang) Belting Ltd. production facility in China is founded and commissioned (photo).
Extension of the production facility for thermoplastic power transmission belts and machine tapes in Wallbach, Switzerland.
Commissioning of the world’s largest plastic calender for coating conveyor and processing belts (production width 4.5 m).
Commissioning of the European fabrication center in Malacky, Slovakia.
New corporate and management culture with a global outlook: Siegling Belting becomes Forbo Movement Systems.
Takeover of the PVC conveyor belt segment from Fenner Dunlop (Georgia Duck) and marketing of the new product group under the Transtex brand name.
Development of a conveyor belt (Amp Miser™) with a particularly low friction coefficient that dramatically cuts energy consumption.
Forbo Siegling develops a bio-degradable conveyor belt made of renewable materials.
Commissioning of a new 5-meter-wide machine to coat conveyor and processing belts in Hanover.
Opening of a new site in Pinghu, China, with production/fabrication, sales and management.
The centenary.
An exceptional milestone for our company and all the people who work in it.
Production of a new Fullsan homogenous belt type starts in Hanover, Germany.