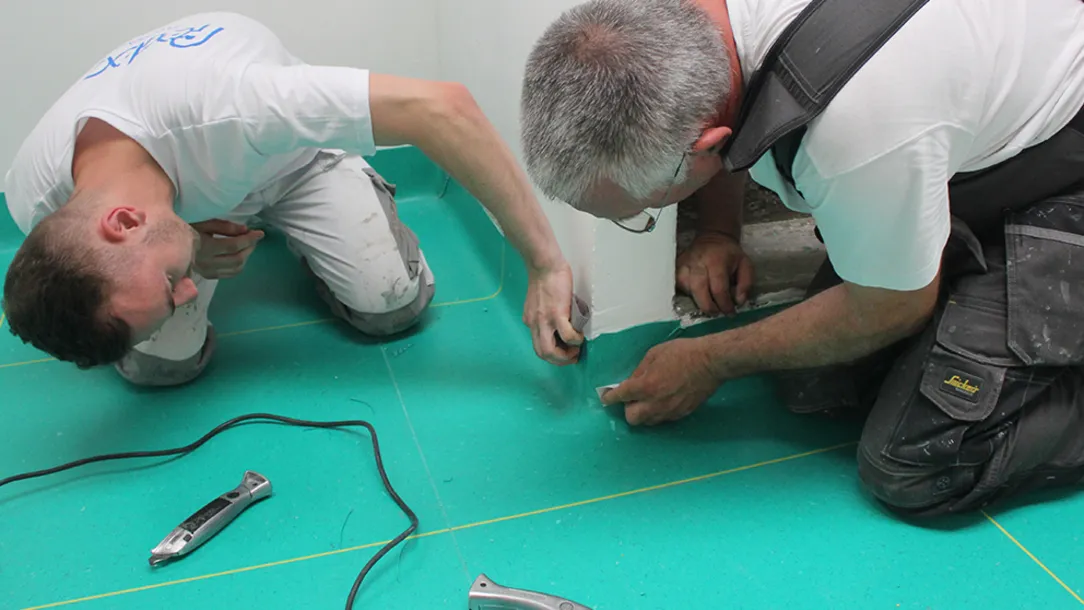
« Des produits comme Sarlon trafic modul’up permettent, dans des cas bien précis, de s’affranchir de l’obligation pour les poseurs de revêtements de sol, de porter des équipements de protection individuelle (EPI) » Mais Jean-François Lacoste, responsable technique et environnement du fabricant Forbo, est catégorique : « en aucun cas l’entreprise ne peut s’abriter derrière la seule utilisation de nos produits pour prononcer cette dispense ».
L’expert nous rappelle ici le processus à suivre. « Pour commencer, il faut suivre une formation spécifique sur les interventions en milieu amianté, pour les chantiers en sous-section 4. Cet enseignement doit permettre à l’entreprise d’établir des procédures standards, appelées modes opératoires, qu’elle va soumettre aux autorités représentant le Ministère du Travail (DIRRECTE) et celui de la Santé (CARSAT).
Une fois ces méthodes de travail validées, il est impératif de réaliser un chantier test, pour chaque procédure définie. « Celui-ci va permettre de vérifier que les niveaux de dégagement de poussières amiantées ne dépassent pas les seuils admissibles, de 5 fibres par litre ». Car ce sont eux qui fixent la limite au-delà de laquelle l’EPI devient obligatoire.
Parmi les éléments qui vont permettre de « tenir » cette limite, l’utilisation d’un revêtement à poser en recouvrement et sans colle, comme Sarlon trafic modul’up, est évidemment un plus. Mais il y a d’autres exigences à respecter. «Ainsi, se servir d’une lame croche plutôt que d’une lame droite, permet de ne pas endommager le support, donc de ne pas dégager de poussières ». Le poseur prendra également soin, lors de ses éventuels percements de trous (pour les seuils de porte par exemple), d’utiliser cette fois un EPC (équipement de protection dit collectif car il protège l’ensemble des personnes à proximité, public compris) : « Dans ce cas, ce pourra être un aspirateur avec un embout adapté et un système d’aspersion de liquide qui fixe les poussières avant l’aspiration ».
Forbo a réalisé un chantier test avec son produit, en équipant tous ses opérateurs d’EPI. Le niveau de fibres dans l’air est resté égal à zéro pendant tout le processus. « En théorie, il est donc possible de se passer de ces équipements de sécurité » admet Jean-François Lacoste. « Après, cela dépend de la stratégie de l’entreprise vis-à-vis de la santé de ses collaborateurs ».
La démarche suivie par le fabricant, est détaillée dans un document tenu à la disposition des artisans et des entreprises qui souhaiteraient s’en inspirer pour établir leur propre mode opératoire. Jean-François Lacoste est cependant très clair : « en aucun cas il ne peut s’agir d’un simple copier/coller de notre méthode. La réglementation est extrêmement claire sur ce point. Chaque entreprise doit produire sa propre démarche ».
En résumé :