Primary Processing
We supply the right belt solutions for all core primary tobacco processes like slicing, conditioning, casing, flavoring, cutting, drying and expanding, as well as feeding the cigarette machines.
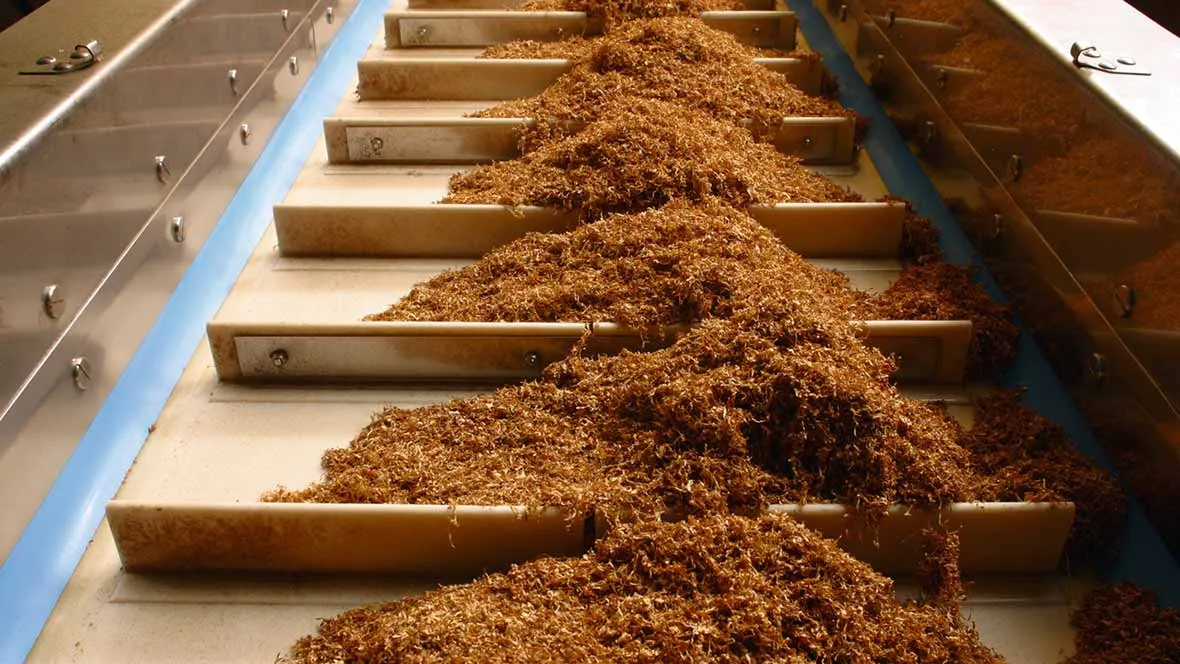
The TT suffix (TT = Tobacco Type) is added to the name of all Siegling Transilon belt types suitable for the tobacco industry. All tobacco types are food safe and pyrolysis compliant. Only conveyor belts made wholly of polyolefin, polyester or silicone fulfill the stringent requirements the tobacco industry places.
The tobacco industry demands the usage of conveyor belts that don’t form any products like nitrogen, sulphur, chlorine or fluorine that are hazardous to health during combustion. This is verified by pyrolytic cleavage, i.e. by burning the belt material at 800°C in the absence of oxygen. The mass fractions of the combustion products are then identified.
The FDA's and EU’s plastics regulations on direct contact with food protect consumers from substances which present a health risk. When conveying tobacco, unwanted substances could be transferred to the tobacco. Belt manufacturers don’t just have to comply with the regulations, but also need to indicate compliance on conformity declarations. Which we do of course provide for all belts in our tobacco range.
Laterally stiff conveyor belts make belts flatter and the forming of creases more difficult. This characteristic is vital, particularly in wide belts or belts for swan-neck conveyors. A special type of fabric with multifilament warp threads and monofilament weft threads make the belts laterally stiff.
Laterally soft belt characteristics encourage troughability in conveyor belts. This characteristic is essential in troughed conveyors. In this case fabric designs are used where warp and weft are flexible multi-filaments.
Release characteristics depend on the physical nature of the top face, the top face pattern and the type of products conveyed (greasy or watery). Coatings with low surface tension, such as polyolefin types, have a natural anti-adhesive effect on polar products. Special coating patterns influence product release because the contact area to the product is changed. We can offer a conveyor belt solution with the optimum release characteristics for any product.
Conveyor belts fitted with profiles for inclined conveying at a steep gradient are an alternative to metal rakes and therefore save costly set-up times. Polyester profiles are available in several shapes and dimensions and some of them can be supplied as roll material.
Ref. No. 318 | Issue 06/20
(PDF | EN | 807 KB)
(10–17 mm height)
(20–60 mm/10 mm height)
(20–100 mm height)
(max. 80 mm height)
A sidewall range, especially for the tobacco industry’s requirements, is available for inclined and steep tobacco conveying. There is a choice of polyester sidewalls, 40 mm to 80 mm in height.
Ref. No. 120 | Issue 08/12
(PDF | EN | 204 KB)
Ref. No. 318 | Issue 06/20
(PDF | EN | 807 KB)
Skirt belts are used to keep fine, dry tobacco on the belt. Which skirt belt is suitable depends mainly on the actual operating conditions and the surface of the belt. Forbo Movement Systems supplies innovative and efficient solutions tailored to customer preferences.
Curtains/covers are always used when substantial dirt (dust) can occur, e.g. at crossover points between two conveyors, or where vapor is produced, e.g. in conditioning drums. Forbo Movement Systems can offer alternative options in blue or beige.
Gentle and effective belt cleaning with polyester scrapers. In contrast to rigid scrapers made of metal or hard plastic, Forbo scrapers are not just gentle to the surface of the belt, but to the splice too.
Article No.: 880066 | Issue 04/18
(PDF | EN | 177 KB)
Smartseal belt edge sealing prevents oil, grease, water and therefore bacteria from entering the belt. Fluff protruding at the belt edges is reliably prevented. This sealing method is successfully used to handle the exacting demands placed on the hygiene of conveyor belts made of synthetic materials and with fabric tension members.
Ref. No 247 | Issue 03/17
(PDF | EN | 145 KB)
Hydrolysis is generated when steam, high pressure and high temperature occur. However, due to their molecular chains, certain plastics like polyolefin or PVC offer very high resistance to hydrolysis. But when damp and hot products are conveyed, or steam cleaning is carried out, hydrolysis can even take place in these plastics. Then splits in the top face or delamination occur. The result of hydrolysis is a drop in mechanical strength.