Tire Industry
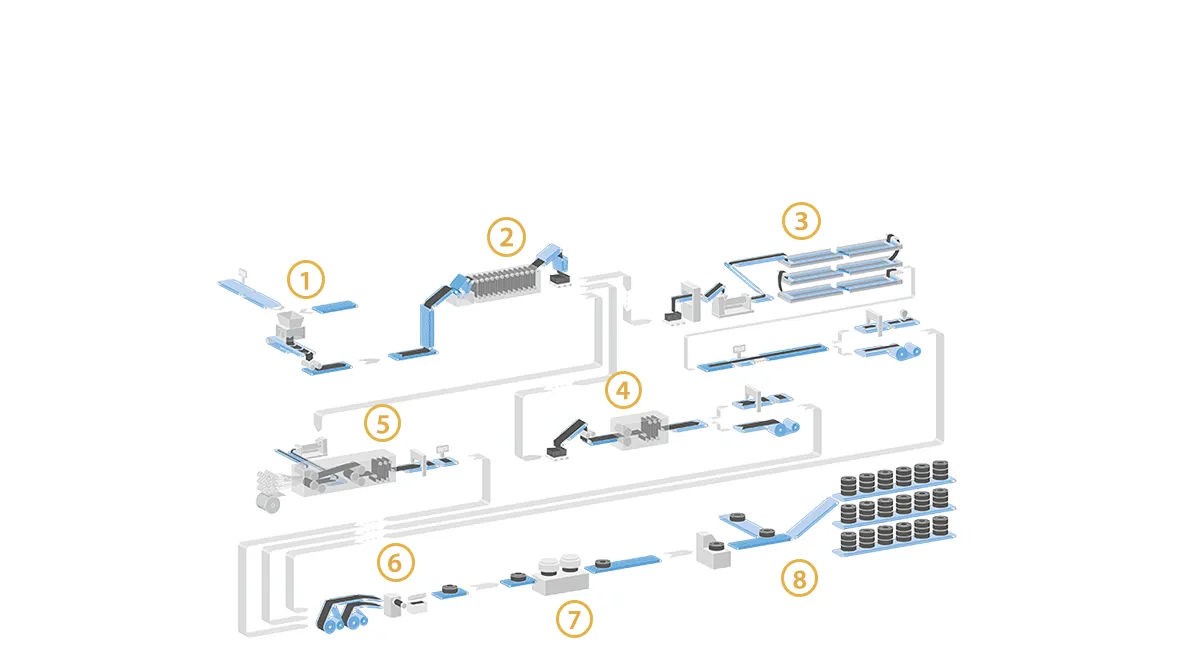
Each tire can contain up to 10 different rubber blends.
The blend determines the subsequent characteristics of various tire components. In addition to rubber and fillers, numerous chemical additives are heated and combined with one another as activators and blending aids etc.
Technical Requirements of the belts
The belts must be exceptionally robust and resistant to incisions, have good release properties and be able to withstand the chemical additives. In some blending processes, water has to be conducted away via the belt.
Directly after the blending process, the finished blend has to be conveyed at a product temperature of up to 175 °C.
Our Solution
Forbo Movement Systems supplies both fabric-based belts (Siegling Transtex, Siegling Transilon) and plastic modular belts (Siegling Prolink) for individual sections of the compounding facility. This portfolio offers optimum belts for any compounding facility.
Different surface patterns on the belts decrease the contact area
to the blend and improve the release properties of the hot and sticky rubber. Resilient coatings and robust fabric designs ensure long services lives and smooth operations. Our PVK150 MF BXB-NA black FR (Siegling Transtex) is used after the kneader and is 100% silicone free.
Other Information
The fabric-based types (Siegling Transtex, Siegling Transilon) are easy to splice with mechanical wire-hook or clamp fasteners.
Downloads
You can find detailed information on the relevant products in the Siegling Transilon Conveyor and Processing Belts overview, Ref. No. 224, Siegling Transtex Conveyor Belts, Ref. No. 214 and Siegling Prolink Modular Belts, Ref. No. 800.
Feeder belts convey the hot rubber sheet from the compounding facility into a dip tank. The sheet is brought up to ambient temperature in the cooling section. A pendulum places the material on pallets in specified batch lengths/weights.
Technical Requirements of the belts
The sheet is conveyed at large angles of incline (in some cases vertically) in front of and behind the cooling section. In addition to chemical resistance, good release properties and exceptionally good grip
are vital at this step in the process. When the rubber is immersed in the dip tank, the belt needs to be consistently waterproof and have a large open area.
Our Solution
The Prolink series 8 modular belt was developed for industrial applications and is the number one choice for conveying in this area. The robust modules have just a one-inch pitch and come in various designs and materials. Each belt can be customized to the type of conveying concerned.
PA-HT capable of withstanding temperatures of up to 155 °C can convey the sheet while it’s still hot. Different surface patterns cut the contact area to the sheet and offer good release properties. The belt offers excellent grip and with rounded ribbing also conveys the rubber sheet gently. Belts with large open areas make immersing the rubber in the dip tank especially efficient.
Other Information
Series 8 Prolink plastic modular belts can be quickly made endless on the conveyor. It’s also easy to replace damaged modules or shorten belts.
Downloads
You can find detailed information on the relevant products in the Siegling Transilon Conveyor and Processing Belts overview, Ref. No. 224, Siegling Transtex Conveyor Belts, Ref. No. 214 and Siegling Prolink Modular Belts, Ref. No. 800.
Two very different sub-processes come together at this step of the process. First of all, the rubber sheet is extruded and injected through dies in defined cross sections from which tread and sidewalls are made later on. After passing through a cooling tray, the strips are either cut to length ready for tire building or rolled up.
Technical Requirements of the belts
The various sub-processes require the belts to have specific characteristics. Some feeder belts to the extruder must be suitable for metal detectors. Behind the extruder, the belt needs to be able to withstand temperatures right up until cooling tray and have good release properties, it must also be possible to use it under water and be exceptionally resistant to incisions.
Our Solution
Forbo Movement Systems offers both fabric-based types (Siegling Transtex, Siegling Transilon) and plastic modular belts (Siegling Prolink). Each extruder and cooling line can be fitted from this portfolio to produce superior results.
We offer two robust Siegling Transilon types that can be used in metal detectors. Siegling Prolink series 8 and 10 belts with a large open area provide excellent support during the cooling process in the cooling tray and when the water is subsequently blown out. For all other functions, Forbo Movement Systems offers a wide range of patterned belts with good release properties and resistance to incisions that are selected to suit the machinery and process concerned.
Other Information
Series 8 and 10 Prolink plastic modular belts can be quickly made endless on the conveyor. It’s also easy to replace damaged modules or shorten belts. The fabric-based types (Siegling Transtex, Siegling Transilon) are easy to splice with mechanical wire-hook or clamp fasteners.
Downloads
You can find detailed information on the relevant products in the Siegling Transilon Conveyor and Processing Belts overview, Ref. No. 224, Siegling Transtex Conveyor Belts, Ref. No. 214 and Siegling Prolink Modular Belts, Ref. No. 800.
The calendering process produces the tire’s inner liner and its carcass. The material (the inner liner or the carcass with the fabric/steel cord positioned between two layers of rubber) is heated up and rolled to the requisite thickness. After passing through a cooling section, the strips are either cut to size ready to build the tire and stacked or rolled up.
Technical Requirements of the belts
Good release properties and superior resistance to temperatures are vital for this process. The cutting process requires belt material that can withstand incisions.
Our Solution
The entire process can be fitted with Siegling Transilon conveyor and processing belts.
Double-ply belts with polyester tension members and urethane-impregnated surfaces as well as NOVO belts made of polyester felt play a pivotal role in ensuring the process is reliable. The surface of the top face makes exact positioning and therefore precise cutting possible.
Downloads
You can find detailed information on the relevant products in the Siegling Transilon Conveyor and Processing Belts overview, Ref. No. 224, Siegling Transtex Conveyor Belts, Ref. No. 214 and Siegling Prolink Modular Belts, Ref. No. 800.
For the tire carcass and steel belt, textile fibers or steel cords are covered with a layer of rubber during the calendering process. A strong bond between these materials is vital to ensure that the tire is safe to drive on and performs well. The components are either cut to size ready for tire building and stacked or rolled up.
Technical Requirements of the belts
Good release properties and superior resistance to incisions are required at this step in the process. Furthermore, because the components are cut to size accurately, the belts need to be able to retain their dimensions and offer good grip in order to achieve exceptional positioning accuracy.
Our Solution
Siegling Transilon conveyor and processing belts and Siegling Prolink modular belts can be selected specifically for particular machinery or processes.
Double-ply or three-ply Siegling Transilon belts with strong tension member fabric made of polyester offer the required dimensional stability. Their smooth surface (made alternatively of different materials and in various thicknesses) offer reliable grip and exceptional resistance to incisions. The form-fit drive of Siegling Prolink plastic modular belts enables the tire components to be positioned precisely in various processes.
Other Information
Stringent fabrication tolerances regarding the belt width, splice’s thickness and quality are vital when preparing the tire components.
Downloads
You can find detailed information on the relevant products in the Siegling Transilon Conveyor and Processing Belts overview, Ref. No. 224, Siegling Transtex Conveyor Belts, Ref. No. 214 and Siegling Prolink Modular Belts, Ref. No. 800.
The prefabricated components are used for tire building. They are either assembled manually or automatically on a drum. The tire is then ready for vulcanization that turns it into an elastic and durable product.
Technical Requirements of the belts
In addition to good release properties, automatic positioning of each of the tire components requires excellent dimensional stability and grip. This is the only way of ensuring precise positioning. Because space is at a premium, only small return diameters are often possible.
Our Solution
Siegling Transilon conveyor and processing belts, Siegling Prolink modular belts or Siegling Proposition timing belts can feed the components with the required precision and be adapted to the space available. The Prolink modular belt series 8 was custom-developed for industrial applications and is perfect for conveying the ready built unvulcanized tire.
Multi-layer Siegling Transilon belts with polyester tension members offer the required dimensional stability and surfaces with reliable grip. Siegling Prolink belts with non-slip surfaces can also be used. With its small pitch, series 4.1 makes small return diameters possible. Siegling Proposition timing belts (PAR/PAZ) can handle exceptional positioning requirements.
Other Information
Stringent fabrication tolerances regarding the belt width, splice thickness and quality are required for tire building.
Downloads
You can find detailed information on the relevant products in the Siegling Transilon Conveyor and Processing Belts overview, Ref. No. 224, Siegling Transtex Conveyor Belts, Ref. No. 214, Siegling Prolink Modular Belts, Ref. No. 800 and Siegling Proposition Timing Belts, Ref. No. 245.
The uncured tire is vulcanized under heat and pressure in a curing mold. In the process, the tire components combine to form an elastic and resilient unit. The tread is formed in this process.
Technical Requirements of the belts
Exceptionally robust belts are required for feeding in and discharging the tires. As the haul-off belts also act as a cooling section, they need to be able to withstand temperatures > 100 °C.
Our Solution
Depending on the machinery concerned, the Forbo Movement Systems range offers both fabric-based types (Siegling Transtex, Siegling Transilon) and plastic modular belts (Siegling Prolink) for these functions. The rollers on plastic modular belts with Roller Top surfaces allow frictionless conveying of the hot vulcanized tires from the sides and onto the accumulation belt.
Robust, fabric-based belts ensure long service lives and smooth operation throughout. They come either with durable coatings or impregnations.
Siegling Prolink series 8 types with large open areas improve the cooling process.
Other Information
Series 8 Prolink plastic modular belts can be quickly made endless on the conveyor. It’s also easy to replace damaged modules or shorten belts.
Downloads
You can find detailed information on the relevant products in the Siegling Transilon Conveyor and Processing Belts overview, Ref. No. 224, Siegling Transtex Conveyor Belts, Ref. No. 214 and Siegling Prolink Modular Belts, Ref. No. 800.
After checking the quality of the vulcanized tires, they’re stored in the dispatch warehouse where orders are then assembled. Tires are often conveyed individually to start with and then stored on pallets on high-bay storage systems.
Technical Requirements of the belts
Tire handling includes the typical functions encountered in logistical processes: horizontal, inclined and accumulation conveying as well as pushing goods on and off belts from the sides. In addition to a robust belt design and superior tensile strength, various surface characteristics and friction coefficients are required. Considering the high number of goods taken to and removed from storage daily, the entire operation needs to function smoothly.
Our Solution
Forbo Movement Systems offers belts dedicated to each of the types of conveying. Both fabric-based types (Siegling Transtex, Siegling Transilon) and plastic modular belts (Siegling Prolink) are used. This portfolio can handle every stage of tire logistics to perfection.
Long conveyors are no problem for hard-wearing Siegling Transilon and Siegling Transtex belts with superior tensile strength.
The type of surface required can be picked to suit the function in question. Siegling Prolink series 8 modular belts fitted with rollers are ideal for accumulation conveying and pushing goods on and off the belts at the sides. This solution is especially good at moving the tires lengthways and sideways on the conveyor.
Other Information
Series 8 Prolink plastic modular belts can be quickly made endless on the conveyor. It’s also easy to replace damaged modules or shorten belts.
Downloads
You can find detailed information on the relevant products in the Siegling Transilon Conveyor and Processing Belts overview, Ref. No. 224, Siegling Transtex Conveyor Belts, Ref. No. 214 and Siegling Prolink Modular Belts, Ref. No. 800.