How fish is produced
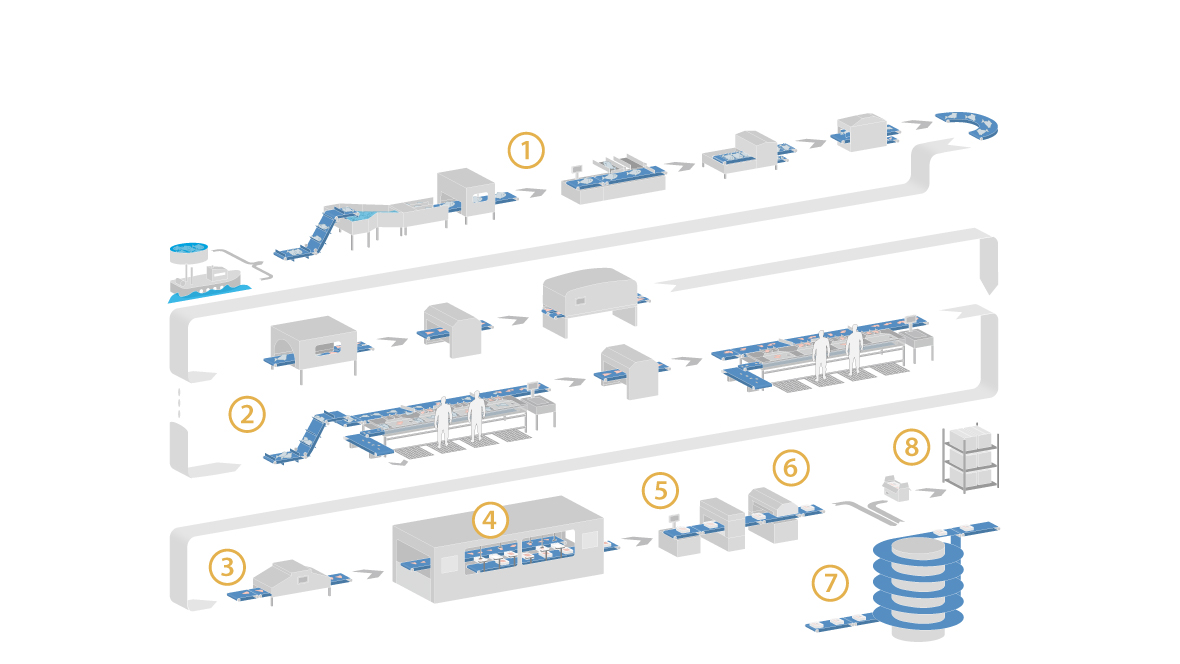
The world of fish processing is multifaceted. Finding conveyor and processing belts to match machines and equipment is complex. But that’s where we come in. We know that your demands on conveyor belts are rigorous. Scrupulous hygiene, the ability to withstand extreme temperatures, large open areas and compatibility with modern detection systems are crucial.
Our conveyor belts meet the fish processing industry’s exacting hygiene requirements. As a result, we can ensure that all steps in the process go as planned. And you can focus on key competencies – your fish products’ quality and freshness.
The machinery used for primary processing is very different. Its configuration depends on the origin of the fish (oceans or fish farms), the species, subsequent processing stages and other factors. Which is why the sequence and function of each step, from slaughtering to gutting the fish, differs depending on our customers’ machinery.
All work can also be carried out on the trawler itself in confined spaces.
During primary processing, fish from farms or those caught in oceans or rivers are stunned, slaughtered, and bled. They are then weighed, sorted, deheaded and gutted if necessary. Customers processing farmed fish frequently want a high degree of automation and combine these steps in one single station.
Technical Requirements of the Belts
Easy rinsing of fish requires belts with large open areas, particularly during slaughtering, bleeding and washing. These belts allow water to drain off quickly. To stop fish slipping and ensure even product spread on the belt, flights are required during inclined conveying and separation processes. Compact curved conveyors are practical space savers on trawlers. Greater automation also means greater requirements on precise and slip-free positioning of the fish. All belts must be exceptionally abrasion resistant and easy to clean. Abrasion-resistant belts have long service lives and withstand the often tough conditions that prevail in fish processing. Easy-to-clean belts mean compliance with high hygiene standards and minimize contamination risks. Therefore, they prevent bacteria, residues and odors occurring that could affect fish quality and safety.
Our solution
For slaughtering, bleeding, and general conveying, we recommend Siegling Prolink plastic modular belts from series 6.1 with a 50 mm (2 in) pitch and very large open areas. On request, we can fit flights and side guards to plastic modular belts, or supply belts in temperature-resistant polypropylene (PP). Products made of polypropylene can withstand extreme cold and heat. They also have superior resistance to cleaning agents.
Siegling Prolink curved belts make very small curve radii possible where space is limited. Prolink plastic modular belts for the food sector have exceptionally easy-to-clean shapes (HACCP designs). In combination with strong polybutylene terephthalate (PBT) hinge pins, they have outstanding service lives.
Alongside plastic modular belts, homogenous belts from the Siegling Fullsan series are also an option for the following steps. The form-fit sprocket drive, teeth on the belt’s underside and patterns and profiles on the top face guarantee excellent positioning accuracy. Siegling Fullsan homogenous belts come Flat (FLT) friction-driven, Positive Drive (PD) and form-fit Center Drive (CD) versions.
All belts are EU/FDA compliant and designed to meet high hygiene standards. They’re very easy to keep clean with all standard detergents.
Contact us if you’d like to know more
More steps are required to prepare fish for consumption and improve the quality of the final product.
The fish is pre-filleted and deboned, then skinned and finally trimmed and cleaned. This is done automatically, semi-automatically or manually in all sorts of machinery configurations.
Technical Requirements of the Belts
Belts with different open areas are required for rinsing between steps. They help water, fish waste and other contaminants to drain away efficiently. To prevent fish fillets from slipping on belts, flights are required for inclined conveying. Some automatic processing stations require precise positioning of the fish so it’s cut properly and in the right size further down the line. The hygiene demands on all belts on the production line are very high.
Our solution
We enhance your processes by providing conveyor belts geared to your machinery, equipment and processes. For conveying tasks in and between stages and during rinsing, we offer Prolink plastic modular belts with various pitches, open areas, profiles and side guards. Where space is at a premium, Prolink curved belts enable very small curve radii. Prolink plastic modular belts for the food sector have exceptionally easy-to-clean shapes (HACCP designs). In combination with strong polybutylene terephthalate (PBT) hinge pins, these belts have outstanding service lives.
We can also offer our Siegling Fullsan series of homogenous conveyor belts made of TPU. To guarantee superior positioning accuracy, Siegling Fullsan homogenous belts come in Positive Drive (PD) and Center Drive (CD) with form-fit drive.
PU-coated belt types from the Siegling Transilon series are another option. These can have patterns and profiles on the top face.
We recommend our PU-coated Transilon belts with Smartseal belt edge sealing for hygiene-critical applications.
All belts are EU/FDA compliant and designed to meet high hygiene standards. They’re very easy to keep clean with all standard detergents.
Contact us if you’d like to know more
To ensure only perfect products are portioned and packaged, fish are usually inspected thoroughly beforehand. Systems need to detect fish with defects such as bones, blood stains and poor trimming, remove them from the process, or send them back for reprocessing. At the same time, quality can be monitored between different process lanes, batches, and shifts. Inspections are normally carried out with X-ray equipment and/or fluoroscopy machines.
Technical Requirements of the Belts
To make sure all the fish is fully and properly screened, positioning accuracy is vital for belts are used in X-ray equipment. In fluoroscopy machines, the belts’ light permeability and homogeneity is crucial to allow reliable detection of flaws or foreign bodies. All belts need to meet stringent hygiene requirements.
Our solution
We can offer numerous belts from several product groups for diverse inspection systems.
For instance, Prolink Siegling plastic modular belts for the food sector with exceptionally easy-to-clean, HACCP-compatible shapes. Or our homogenous belts from the Siegling Fullsan series, as well as our Siegling Transilon belts with PU coatings and optional Smartseal belt edge sealing.
We can supply all types with top-face patterns to match the application. Our portfolio also includes a range of transparent Transilon belts with exceptional light permeability for fluoroscopy machines.
All belts are EU/FDA compliant and designed to meet high hygiene standards. They’re very easy to keep clean with all standard detergents.
Contact us if you’d like to know more
After being weighed and sorted, the fish are portioned into consumer-ready products. Trays, boxes, or bags are filled with the required quantities. These steps are usually automated, but semi-automatic or manual in some cases. Depending on the machinery and product, the portions are then labeled and repackaged accordingly.
Technical Requirements of the Belts
All the belts need to be food grade and easy to clean. But other characteristics are also crucial, such as uniform thickness during weighing to ensure exact results. Good product grip to position the fish accurately during cutting is also a must. (see point 6 on Check-Weighing).
Our solution
Special belts for check-weighers with very precise splices of the same thickness help prevent errors in compiling exact portion sizes (see also point 6 on Check-Weighing). We can supply belts with excellent grip, tailored to the application. As a result, we help to guarantee flawless processes and perfect positioning.
Prolink plastic modular belts for portioning have very easy-to-clean shapes (in an HACCP-Design). In combination with sturdy polybutylene terephthalate (PBT) hinge pins, they have long service lives.
We can also supply homogenous belts from the Siegling Fullsan series. The Positive Drive (PD) and Center Drive (CD) versions have form-fit drive and therefore exceptional positioning accuracy.
Belts from the Siegling Transilon series with PU coating and optional Smartseal belt edge sealing are another good choice. If required, form-fit drive is also possible tension free via rows of holes at the sides.
All belts are EU/FDA compliant and designed to meet high hygiene standards. They’re very easy to keep clean with all standard detergents.
Weight is usually monitored during production via check-weighers integrated in the conveyor belts. As a result, there’s no need to remove the products from the process. Products can either be packaged or unpackaged.
Technical Requirements of the Belts
The belt’s hygiene standard depends on whether packaged or unpackaged fish is weighed. To minimize weighing errors, the quality of the belt and its fabrication need to be outstanding. For instance, belt thickness must be identical – even across the splice – or the splice has to be narrow. To allow small end diameters and achieve very precise weighing results, thin belts are preferred.
Our solution
Multiple types from our Siegling Transilon series of conveyor and processing belts are made in consistent thickness for this application. Exact fabrication guarantees the same surface weight, even in the area where the splice is. What’s more, elastic belts with homogenous product designs and easy-to-clean surfaces are predestined for use in check-weighers.
Our check-weigher belts come in a consistent thickness and with very precise splices, which makes endless belts superfluous. We can apply our Smartseal belt edge sealing to many of our fabric-based belts if hygiene requirements stipulate it. Elastic belt types require no tensioning station because they maintain their natural elasticity.
Contact us if you’d like to know more
Metal detectors are used during final inspections to rule out risks of contamination by foreign bodies. They help guarantee that the final product contains no metallic objects. As a result, food is even safer for consumers and demanding quality standards are met.
Technical Requirements of the Belts
Conveyor belts destined for metal detectors mustn’t contain any metallic components that could alter inspection results. All the belt’s other components, including splices or clips, must equally be metal free so that they don’t impair detection results. Conveyor belts that are the same thickness throughout also guarantee consistent and reliable detection.
Our solution
Depending on the metal detector’s design and sensitivity, we can offer various plastic modular belts from the Siegling Prolink and Siegling Transilon conveyor and processing belt series, as well as homogenous belts from the Siegling Fullsan range. Non-antistatic and colorless belting material is practical for many metal detectors. Plastic modular belts are only used with plastic hinge pins.
We have a wide range of antistatic belts or transparent plastic modular belts for all sorts of detection equipment. Our belts product reliable results, prevent faulty ones and meet the high standards of food processing.
Many sales channels require deep-frozen products. These are necessary to guarantee the quality, availability and safety of food and respond to consumer demands. To do so, the products are cooled down to the required temperature in the final processing stage, either in linear or spiral freezing systems.
Technical Requirements of the Belts
Because the belt material mustn’t become brittle at low temperatures (down to -40°C), it comes in a cold-resistant version. Should damage occur, to minimize downtime it must be easy to repair and guarantee top product quality. To prevent any negative impact on the freezing process, the belt needs to have an open area. Curve-compatible belts are required for spiral freezers.
Our solution
Plastic modular belts made from temperature-resistant polyoxymethylene (POM) and polyethylene (PE) from the Siegling Prolink series are ideal for deep freezing applications. We can offer linear and curve-compatible modules with large open areas. All Siegling Prolink plastic modular belts are designed for top hygiene standards. They are also EU/FDA compliant, which makes them ideal for all food applications.
Prolink plastic modular belts for the food sector also have very easy-to-clean shapes (HACCP designs). Modules made of polyoxymethylene (POM) or polyethylene (PE) have very long service lives for these types of processes. Their large open areas and excellent heat transfer make short cooling sections possible. Curve-compatible Prolink belts with stainless steel hinge pins have no problems with the extreme tensile force in cooling towers.
Contact us if you’d like to know more
This step involves several very different sub-processes. Specific approaches are applied during wrapping, repackaging in boxes and palletizing. Outstanding packaging processes protect products and guarantee quality, safety, and shelf life.
Technical Requirements of the Belts
Multiple parameters specific to the machinery or equipment govern the packaging of fish. To make sure the process is efficient and safe, compliance with these is essential. For instance, the conveyor belts need to have outstanding tensile strength or elasticity. The process and type of conveying determine the technical demands of the processing and conveyor belts.
Our solution
For each of the sub-processes, we can supply fabric-based belts from our Siegling Transilon series and Siegling Prolink plastic modular belts. Robust, durable belts guarantee seamless processes. HACCP-compliant belts enable direct contact with food and outstanding hygiene.
This portfolio has products for any type of packaging machinery. As a result, you’ll be able to exploit your quality and productivity potential to the full.
Contact us if you’d like to know more
The world of fish processing is multifaceted. Finding conveyor and processing belts to match machines and equipment is complex. But that’s where we come in. We know that your demands on conveyor belts are rigorous. Scrupulous hygiene, the ability to withstand extreme temperatures, large open areas and compatibility with modern detection systems are crucial.
Our conveyor belts meet the fish processing industry’s exacting hygiene requirements. As a result, we can ensure that all steps in the process go as planned. Our innovative belts with belt edge sealing (Smartseal) offer superior hygiene, which guarantees the quality and safety of your fish products.
Our HACCP-certified belts are champions in terms of precision and adaptability. They come in a wide range of coatings and patterns to match fish processing’s exacting requirements. These very easy-to-clean belts meet stringent EU- and FDA-standards with ease. What’s more, they ensure first-class efficiency and the high quality of each fish product.
Are you looking for conveyor belts for efficient fish processing? We’d be happy to help find the perfect belts for your applications. And you can focus on key competencies – your fish products’ quality and freshness.
Our specialized service teams support the fish processing industry with 24/7 on-site assistance. We offer professional belt installation, hygienic splicing, reliable emergency repairs, and safety-compliant maintenance. With local presence and industry know-how, we keep your conveyor systems running efficiently – on site, with the right equipment and a single point of contact.
Learn more and get in touch
Any questions about our product for the fish production sector? Then contact us.
To the contact form